What is a Good Miller Continuous Duty Welder
The welding duty cycle is the percentage of a 10-minute interval during which the welding power source can output the rated amperage continuously. The welding machine duty cycle designates how long a welder can output the rated amperage before it needs to cool.
For example, a welder with a duty cycle rating of 200A at 60% can output 200 amps for six minutes before needing to rest for the remaining four minutes of the 10-minute interval.
Here is a good video explaining the essence of it:
The importance of Duty Cycle in welding
Welding machines go into thermal overload mode when you exceed the duty cycle limit while welding. The arc power cuts off while the cooling fan keeps running to help dissipate heat away from the sensitive parts inside your welder.
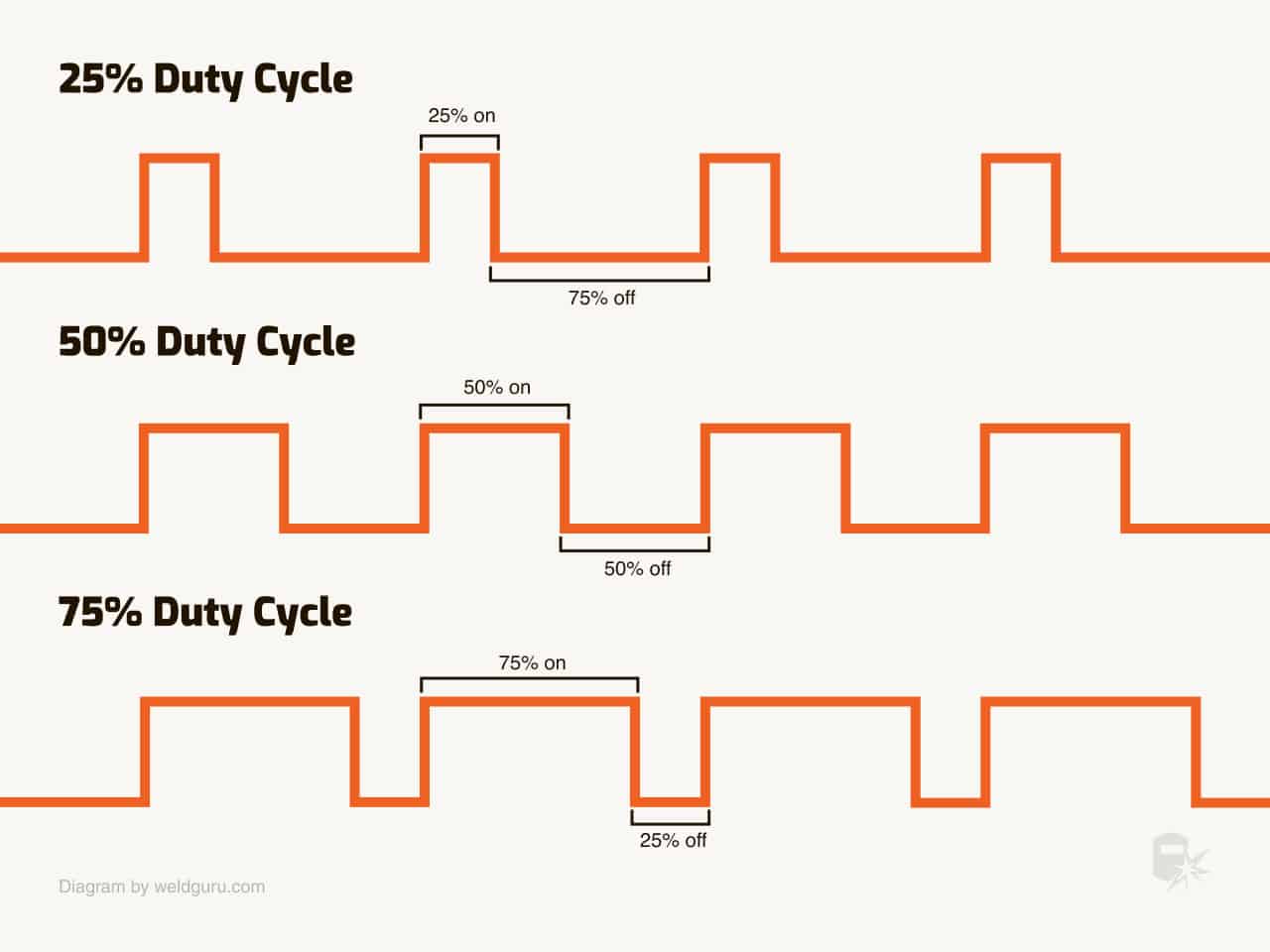
Internal components of welding machines like IGBT transistors, transformers, rectifiers, capacitors, and resistors get hot as you weld. The higher the amperage output, the more heat generated. Any of these parts can fail if the machine is overloaded. So, manufacturers design and test their welders to determine the optimal duty cycle for safe operation.
The duty cycle is an important metric because it gives you a general idea of what kind of jobs the welder can handle. For example, hobbyist welders are typically rated with shorter duty cycles, while professional units have much longer ones.
Is Duty Cycle Always Tested the Same Way?
The duty cycle is not always tested the same way. This creates confusion and an unfair "advantage" among the welding brands.
The 10-minute timeframe for the duty cycle is the industry's gold standard, and most US, EU, and AU manufacturers use it. Still, nothing prevents a brand from rating their welders using a 5-minute timeframe, allowing them to claim a far longer duty cycle. In this example, up to 50% longer.
However, if the manufacturer deviates from the 10-minute rating, they cannot claim that they follow the European standard EN60974-1 or Australian standard AS60974-1 (based on EU standard).
Additionally, the same AS/EN60974-1 standard designates that the testing must be done at an ambient temperature of 40°C after at least two thermal overloads. So, if a brand tests their welders at 20°C, or they don't overload the machine twice pre-testing, they can claim an inflated value.
As you can imagine, testing a cold welder at low ambient temperature results in a higher rating. But, such tests are not genuine. In the real world, the machine must achieve its rated duty cycle even after it hits a couple of consecutive thermal overloads.
So, ensure the welder you buy abides by the AS/EN60974-1 standard. Many welding machines have this standard printed on the specification plate on the back. Check the user manual or contact the brand's customer support if it's not there.
One final note, it's impossible to compare two welding machines if the duty cycles were tested differently. The AS/EN60974-1 standard is widely accepted, and brands that claim high duty cycles without using this standard are likely inflating their numbers. Be careful of such marketing tricks.
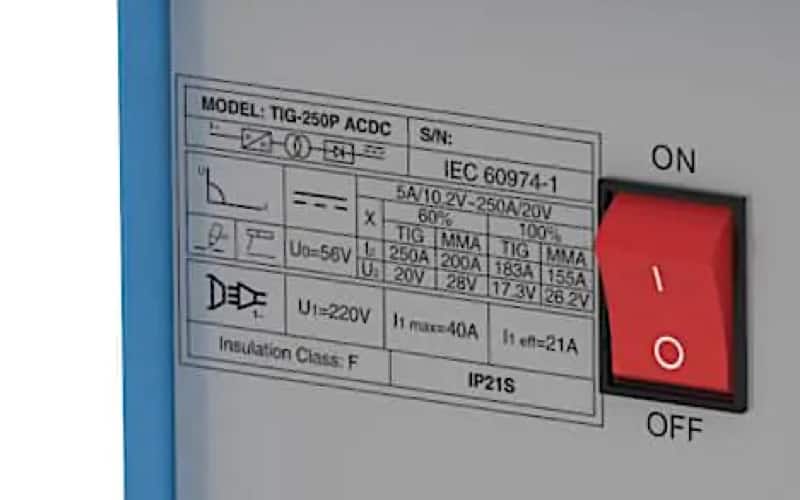
The AS/EN60974-1 standard also demands that the welder's thermal overload protection endures 100 consecutive overloads for units with a 35% or higher duty cycle. Machines with a duty cycle lower than 35% must tolerate 200 overloads. So, if the welder doesn't meet this standard, its internal components may not be high quality.
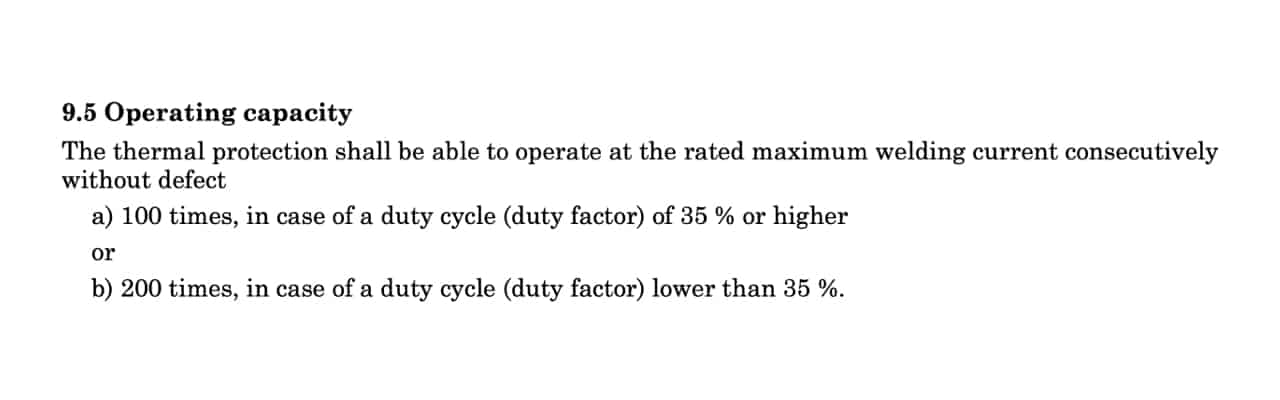
Is Duty Cycle the Best Way to Evaluate a Welder?
The duty cycle is not the single best way to evaluate a welder. There are numerous other factors to consider when choosing your machine. However, the duty cycle is one of the crucial specs to consider.
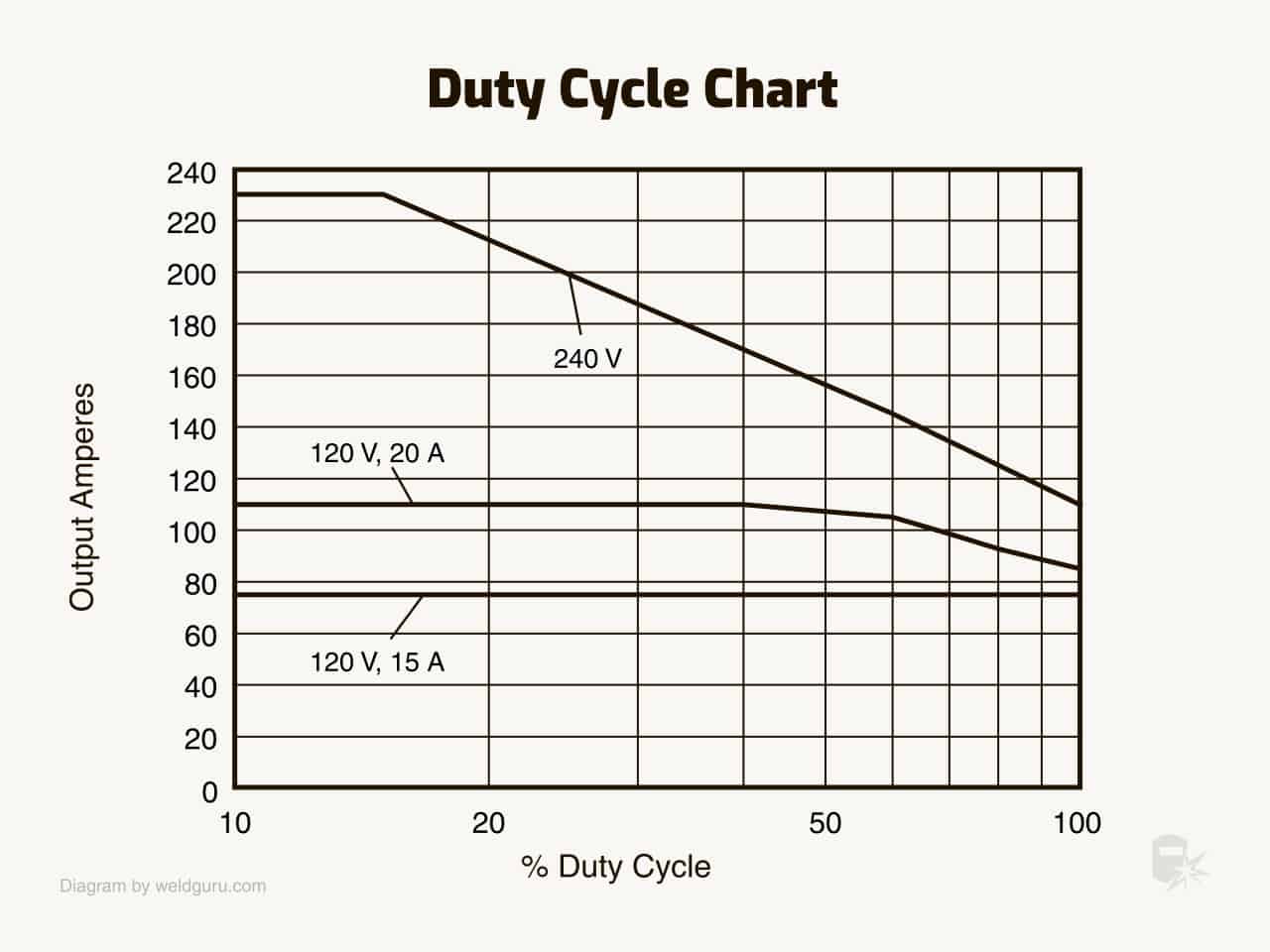
A short duty cycle welder will constantly overheat if you plan to perform high-volume welding at high amperage outputs. Likewise, buying a high-end welder is a waste of money if you are a hobbyist or need a welder for light shop welding.
Besides the duty cycle, you should consider the welder's amperage output range, the included functions, portability, build quality, and most importantly, the warranty. If a welder has a high duty cycle but is warranted for less than a year, it's likely to die faster than you would like.
Additionally, consider that you are unlikely to weld in 40°C ambient temperature after hitting two consecutive thermal overloads. So, whatever machine you buy, you are likely to enjoy a longer duty cycle than the one stated on the label if the manufacturer abides by the AS/EN60974-1 standard.
Take a look at this duty cycle comparison in the video below. All four brands outperformed their rated duty cycles when tested in an actual welding shop. The most probable reasons are the ambient temperature was lower than 40°C, and the welders were cool at the start of testing.
Duty Cycle, Maintenance, and Humidity
Besides ambient temperature, dust and other debris may impact the duty cycle of your welder. If the airflow vents are blocked with gunk, your machine will overheat faster. Plus, if dust "insulates" the sensitive components inside the welder, the heat will be harder to dissipate. The dust layer acts as a blanket. So, ensure the cooling fans are unobstructed and perform regular welder maintenance.
Additionally, humidity can affect heat dissipation and reduce the duty cycle. Ambient air with high relative humidity has lower thermal conductivity, which slows heat transfer from heated elements inside the welder to the atmosphere. If you work in highly humid areas, you may experience a reduced duty cycle.
Duty Cycles for Different Welding Processes
Arc welding processes like MIG, TIG, and SMAW put different demands on the welder. As a result, they have inherent differences that directly influence the duty cycle needs.
MIG Welding Duty Cycle
The MIG welding process uses automated wire feeding and allows continuous welding operation. Since the process doesn't require you to make frequent pauses, MIG welding machines often have long duty cycles.
Of course, if you only perform light sheet metal welding, you will do well with a short duty cycle MIG welder. But, if you plan to weld thick sections with a MIG welder, you should get a high-duty cycle machine.
You should consider the thicknesses you want to weld and the amperage needed to do it. Then buy a welder with at least a 60% duty cycle at your required amperage.
TIG Welding Duty Cycle
The TIG welding process is slow and doesn't require frequent stops. You may need to pause the weld to get another filler metal rod, but that's a short break that won't considerably cool the machine. So, if welding thick sections, get a high-duty cycle welder.
However, most TIG welding applications require less than 100-130A. Many welding machines can run at 100% duty cycle at such low loads. So, if you do precision work on thinner materials, you won't have to worry much about the duty cycle.
Also, welders are not rated for pulsed current output. Professional TIG equipment allows pulsed welding that alternates between high and low amperage output. This results in longer duty cycles because less strain is put on the machine's electrical components. Plus, even if a TIG welder doesn't include a pulse function, using a TIG foot pedal to moderate amperage output when welding also improves the duty cycle length because the average continuous load is lower.
Stick Welding Duty Cycle
The stick welding process allows frequent intermittent pauses as you travel along the joint. Replacing the stick welding electrode, chipping away the slag, brushing the soot and removing fine slag particles, and peening in the welds allow the welding machine to cool. As a result, you can use a shorter duty cycle machine and get most jobs done.
The long pauses while stick welding are one of the reasons that multi-process welders offer the shortest duty cycle for the stick process.
You can get most jobs done with a 150A stick welder with a 40% duty cycle. Stick welding allows deeper penetration than other arc welding processes. So, with some joint preparation and at least 150A of power, you can weld any steel thickness lower than 1/2 in. With a 40% duty cycle, you'll get to weld for about four minutes. You'll likely consume the stick electrode faster than that, and the machine will cool down while you clean the slag and prepare the joint for the next electrode.
What happens When the Duty Cycle is Exceeded?
When the duty cycle of a welding machine is exceeded, the welder will trigger the thermal overload safety feature. Most welders have this safety measure. Still, some welding machines don't, and they may catch fire, or some of their sensitive parts may fry.
Most welding machines have thermocouples inside to monitor the temperature of the internal components. Once the critical temperature is reached, the thermocouple sends a signal to the thermal overload circuitry, which shuts down the power.
Don't pull the welder's power plug if the thermal overload mode is activated. This will turn off the cooling fans, which should keep running to help excessive heat escape.
If you continuously breach the duty cycle, the welder's life span will reduce, regardless of what the manufacturer claims. The internal components and their insulation begin to break down at high temperatures, eventually leading to equipment failure.
So, you should avoid constantly hitting the duty cycle limits. Modern welders use hundreds of tiny components on their printed circuit boards, and a single resistor, capacitor, or IGBT transistor may fry if you push the machine. Plus, many of these components rely on tiny connections the width of human hair. These are sensitive, and constant overheating will cause damage.
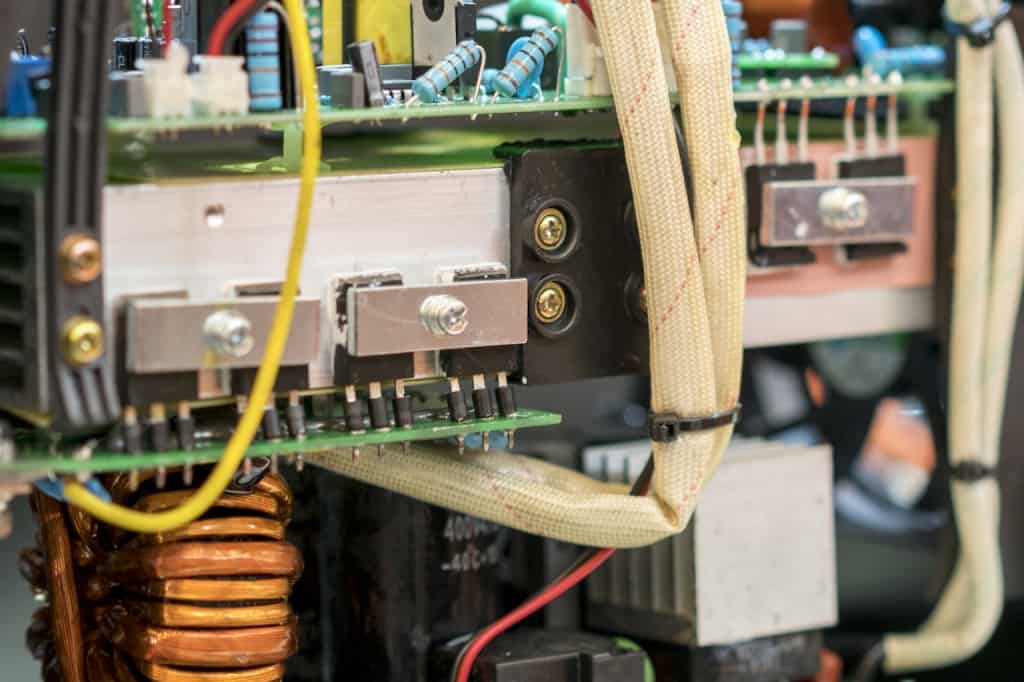
Wrapping It
It's not always possible to directly compare the duty cycles of two welders. Manufacturers may vary their testing methods. So, the comparison doesn't mean much unless you compare brands that follow the same test standard.
Get a welder with a higher duty cycle if your budget allows it. It's better to be safe than sorry.
However, if you don't plan to weld often or make long beads, it's okay to save money and get a less expensive machine. You should prioritize warranty over the duty cycle, especially when a brand claims a high duty cycle but provides a short warranty.
Finally, the duty cycle is not the only thing to consider when purchasing a welder. Ensure that the machine has the power for the thickness you intend to weld and the features necessary for the materials you wish to join.
For example, if you want to weld aluminum, a MIG welder must support a spool gun, while a TIG welder needs to output AC. So, make sure that the machine can achieve what you need first, and then consider the duty cycle.
Source: https://weldguru.com/duty-cycle-in-welding/
0 Response to "What is a Good Miller Continuous Duty Welder"
Post a Comment